Asphalt Shingle Roof Replacement
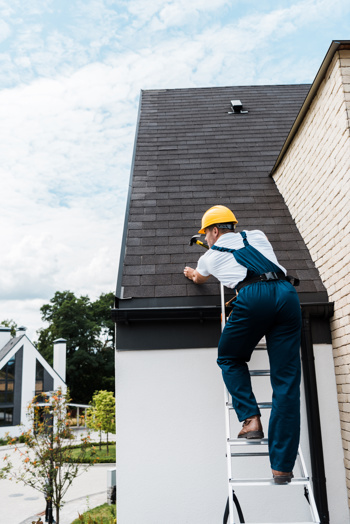
Replacing an asphalt shingle roof is a common and cost-effective solution for maintaining the integrity and appearance of your home. This process not only enhances curb appeal but also provides essential protection against the elements. By understanding the key steps involved, homeowners can ensure a smooth and successful roof replacement project.
- Initial Assessment and Preparation
Before any work begins, a thorough inspection of the existing roof is conducted to assess its condition and identify any underlying issues. This helps in planning the scope of work.
- Removal of Old Shingles
The old shingles are removed in sections, starting from the top and working downwards. This process usually involves the use of roofing shovels to pry up the old shingles and nails.
- Decking Inspection and Repair
Once the old shingles are removed, the roof decking is inspected for any damage such as rot or water damage. Any compromised sections are replaced with new decking material.
- Underlayment Installation
A new underlayment (felt paper or synthetic material) is installed over the decking to provide an additional layer of moisture protection.
- Drip Edge and Flashing Installation
Drip edges are installed along the eaves and rakes of the roof to direct water away from the fascia. Flashing is installed around roof penetrations such as chimneys, vents, and valleys to prevent water infiltration.
- New Shingle Installation
The new asphalt shingles are installed, starting from the bottom edge of the roof and working upwards, ensuring proper alignment and overlap. This step often includes installing ridge vents and other ventilation features.
- Final Inspection and Cleanup
After the shingles are installed, a final inspection is conducted to ensure everything is properly in place. The job site is then cleaned of all debris and leftover materials.
Flat Rubber Roof Replacement
Replacing a flat rubber roof involves a meticulous process to ensure waterproofing and durability for flat or low-slope structures. This type of roof replacement requires specialized materials and techniques to provide a seamless, long-lasting solution against leaks and weather damage. At Peak we've been there and our crews are specialized to make sure your project will last for decades.
- Initial Assessment and Preparation
The process starts with thoroughly inspecting the existing roof to identify any issues with the decking or insulation.
- Removal of Old Roofing Material
The old roofing material is removed, typically using specialized tools to avoid damaging the underlying structure.
- Decking Inspection and Repair
The roof decking is inspected for damage, and any compromised areas are replaced.
- Insulation and Underlayment Installation
If the existing insulation is in good condition, it can be reused. Otherwise, new insulation is installed. An underlayment or a vapor barrier is then applied to protect the roof structure from moisture.
- Drip Edge and Flashing Installation
Drip edges and flashing are installed to manage water runoff and prevent leaks.
- New Rubber Membrane Installation
The new rubber membrane (EPDM, TPO, or PVC) is installed. The membrane is usually adhered, mechanically fastened, or ballasted, depending on the type and specifications.
- Final Inspection and Cleanup
A final inspection ensures the membrane is properly installed and sealed. The site is then cleaned of all debris.
Standing Seam Metal Roof Replacement
Standing seam metal roofs are renowned for their sleek, modern appearance and exceptional durability. This type of roofing system features raised seams that run vertically from the roof's ridge to the eaves, providing a distinct aesthetic and superior protection against water infiltration. The unique design not only enhances the architectural appeal of any structure but also ensures a long-lasting, low-maintenance roofing solution that can withstand harsh weather conditions.
- Initial Assessment and Preparation
A thorough inspection of the existing roof is performed to plan the replacement process.
- Removal of Old Roofing Material
The old roofing material is removed, and the decking is inspected for damage.
- Decking Inspection and Repair
Any damaged decking is replaced to provide a solid foundation for the new roof.
- Underlayment Installation
An underlayment or ice and water shield is installed to provide additional waterproofing.
- Drip Edge and Flashing Installation
Drip edges and flashing are installed to direct water away from the roof.
- Metal Panel Installation
The standing seam metal panels are installed, starting from the bottom and working upwards. The panels are fastened using concealed fasteners to create a sleek appearance.
- Ridge Cap Installation
A ridge cap is installed to protect the roof's peak and ensure proper ventilation.
- Final Inspection and Cleanup
The roof is inspected to ensure all components are securely in place, and the job site is cleaned of all debris.
Replacing a roof, whether it's with asphalt shingles, a flat rubber membrane, or standing seam metal, is a complex process that requires expertise and careful planning. Each type of roofing material has its unique requirements and challenges, but with the right approach, you can ensure a durable and aesthetically pleasing result that will protect your home for years to come.